Plug And Play
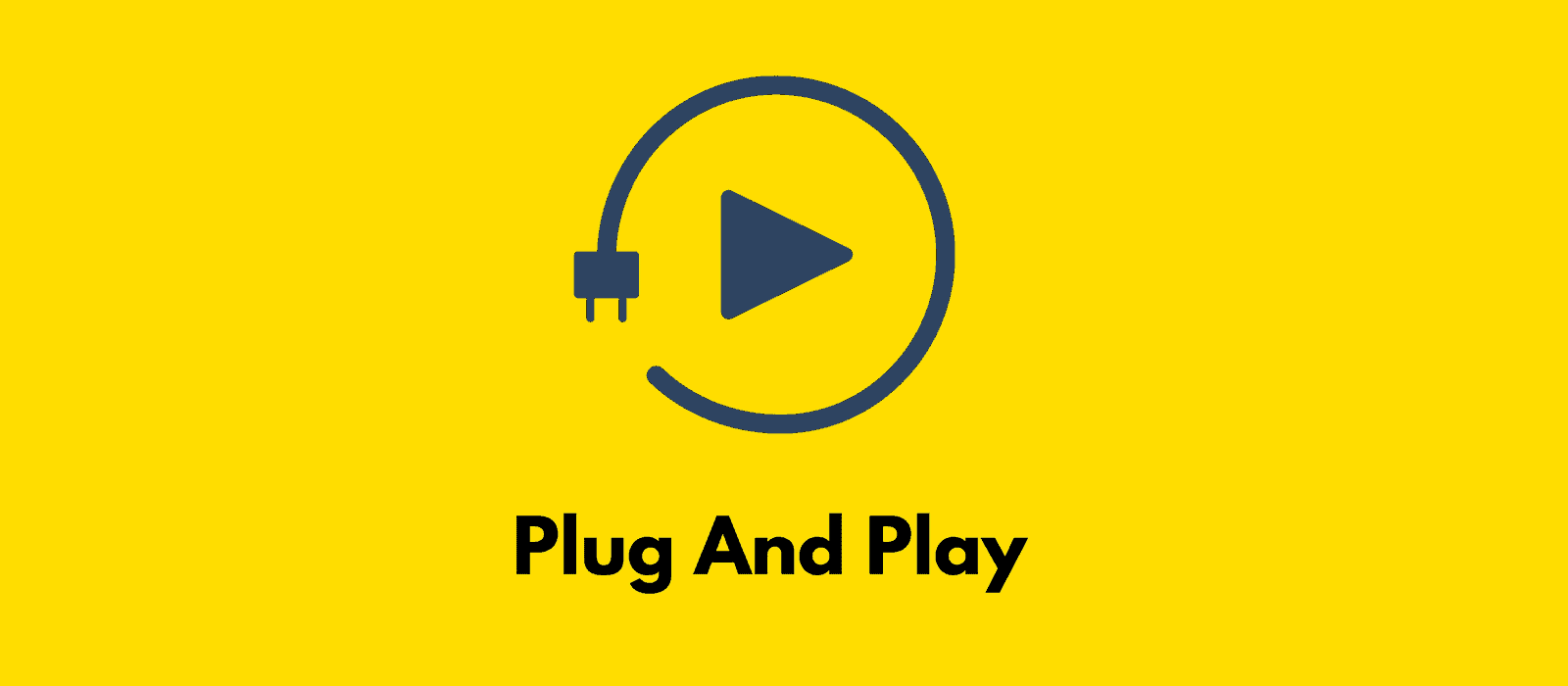
There are just times when due to many different circumstances, CNC programs or tool paths cannot be changed. It could be either time constraints or lack of programming resources at a customer. The team at S&D in such scenarios is very adept & versatile at making the most of the available resources to improve productivity output at our customers.
A case in point, a local aerospace shop has been running a job for many months in 300M High Tensile Strength material. When there was a change in the shop leadership, our salesperson Cesar Garcia was challenged to improve this particular job. Cesar was tasked to bring in an end mill that would improve productivity & tool life without making any changes to the existing CNC program or tool paths.
The job entailed running the part on a CNC Mazak 50 taper vertical machine, machining from solid block of 300M material. The program called for completing both the roughing and finishing operations with the same tool. The original run time per part was 9 hours and required more than 1 of our competitors’ end mills to complete a single part. Inconsistency in tool life was also a major concern causing added cycle time due to abrupt tool breakage.
Cutter Considerations
Cesar, teamed up with our end mill supplier IMCO, and their application specialist Ken Maxfield who after reviewing the customer application, setup and CNC program suggested a IMCO | Part: 0336512 | M525N 3/8 5F .030R enDuro Mill 3/8 x 3/8 x 1/2 x 3 LBS=1-3/8 AlCrNX (imcousa.com).
The M525 enDuro series from IMCO is a definition of versatility and is designed to rough and finish in traditional tool paths and in high-efficiency machining techniques. Ken Maxfield from his past experience of running the tool in 300M knew the M525 5-Flute would be the “go-to” tool that would save S&D’s customer time and money.
The IMCO M525N Series endmill were able to make significant productivity gains at the customer while only making minor changes to the speeds and feed of the CNC program.
Results with the S&D Difference:
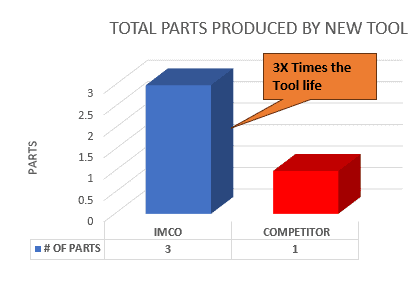
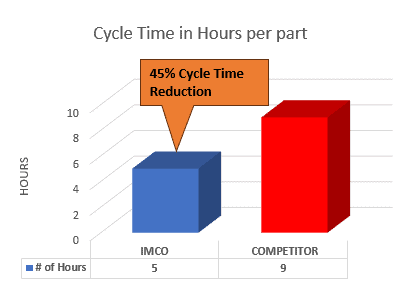
This is an ongoing job for our customer, and even with conservative estimates the results are cost savings of over $500 per part. The new shop manager and the plant manager are very excited to start looking for more opportunities. Challenge our sales team and experience the S&D Difference for yourself!