Time is Money
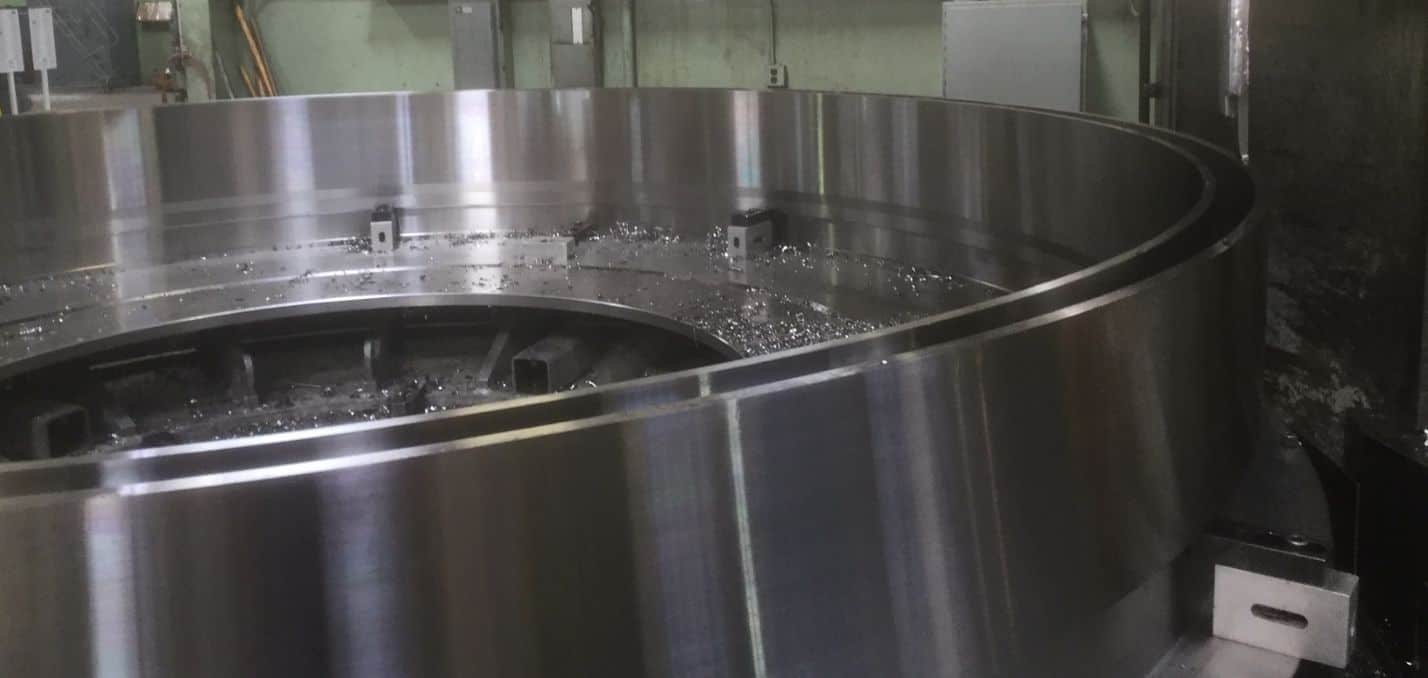
Time is Money
We’ve all heard this expression used many times. In manufacturing, wasted cutting time may be the difference between a losing and highly profitable job.
Case in point: One of our customers has a 150” forged ring, requiring a slot 13” deep, approximately 2.50” wide with a .250” corner radius at the bottom and a finish callout of better than 63rms. On the initial part they used tooling they already had or made themselves. Just the slotting operation alone took 160 hours. Our team at S&D was called in to reduce the time by at least half to make the job profitable again.
Working with one of our custom tool designers at Lovejoy Tool Company, we were able to design, engineer and produce a set of tools with replaceable pockets utilizing indexable inserts. The tooling we designed would rough the entire depth of the slot, finish the walls and floor, finally blending the radius as well.
The first time we put the tools into service was on ring #2. When we started cutting the part the operator couldn’t believe we were even cutting material. We finished the same operation in 55 hours, remember the first part ran 160 hours. Saving over 100 hours per part, at a conservative shop rate of $100 per hour that is a savings of $10,000 per part, every part.
One thing better than saving time is saving LOTS of time and making LOTS of money in the process. They expect to produce at least 2 rings a month, running on multiple machines. We are looking at the remaining operations so the savings can just keep on growing.
We look forward to similar opportunities with this customer and on your shop floor or engineering department.