The S&D Difference
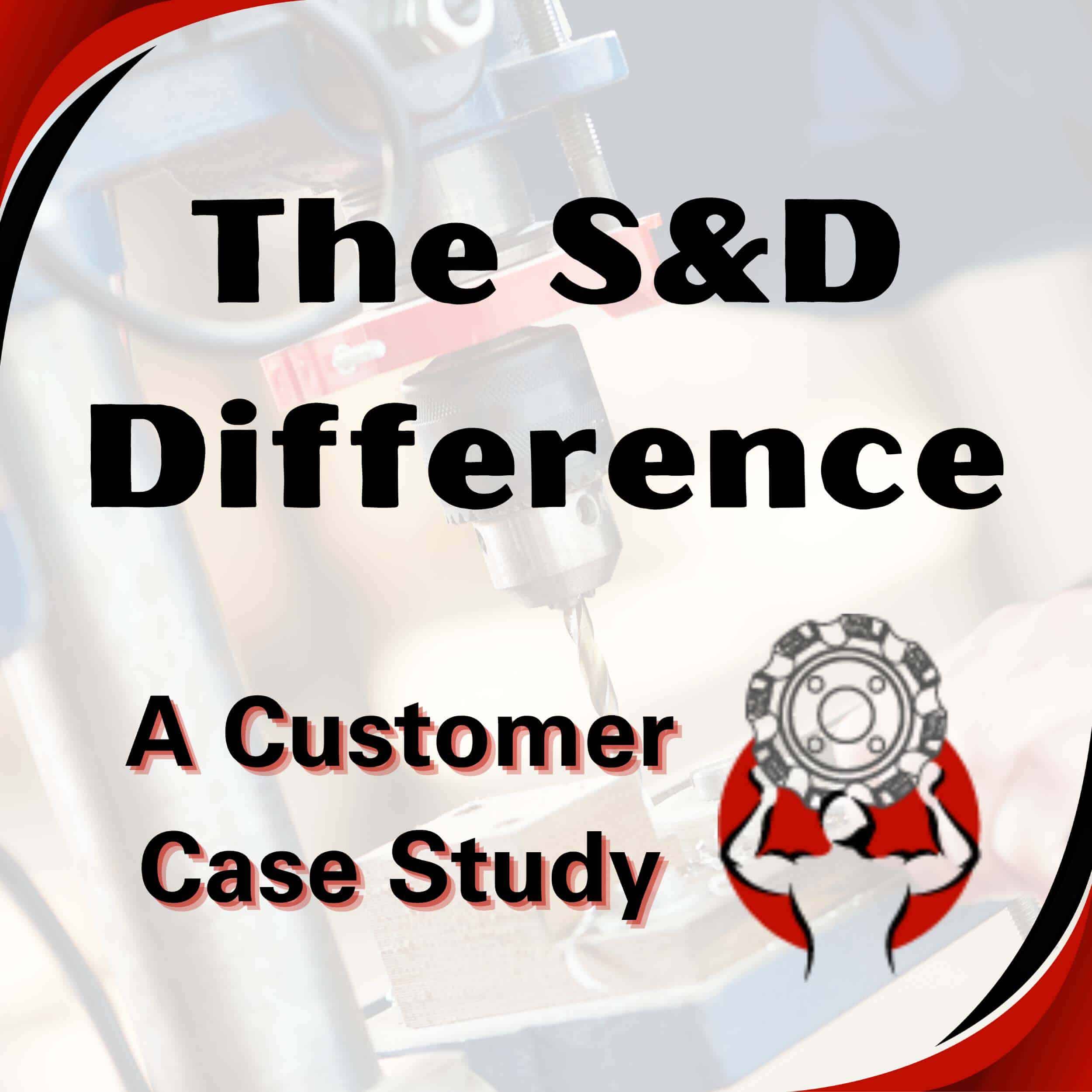
Our customers know they can rely on us to provide solutions to their productivity improvement process.
Case in point
S&D partnered with our customers and suppliers to reduce cycle time to meet production requirements without adding machines or additional personnel, but running other projects.
Scenario
Running on a CNC vertical mill, steel casting, requiring 52 holes. 0.781” diameter through a flange at 1.5” thick. The customer was running an indexable trigon drill offset to finish the hole at a 0.781 diameter. Unfortunately, the drill left a poor finish, requiring re-work. Additionally, the drill would blow out the edges of the exit hole, requiring, again, more re-work. The best feed rate achievable was 1.5 IPM. There were 20 parts to run, and in total run time for this operation with tool changes and rework was over 6 hours.
Solution
we used the new Ingersoll Twist Feed, 3-flute replaceable tip drill. Drilling at 0.7677” one shot no pecking through the flange at 8 IPM. The drill ran flawlessly, completing all 52 holes, improving the finish, and creating no exit issues on the flange. We followed this with Big Daishowa twin bore running at 4 IPM. It had better than 32 finish and held size within + or - 0.002. requiring no rework, parts came off the machine finished.
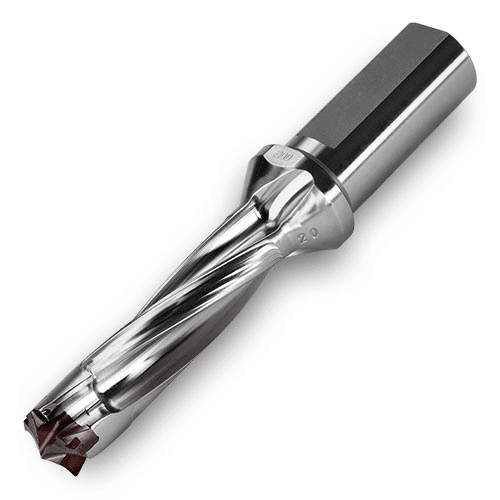
Results
The approximate run time came down to 90 minutes. About a 400% improvement in throughput and productivity gains. With a shop rate on this machine of at least $100 per hour, savings per part are $450.00. The total savings per job are $9,000.00
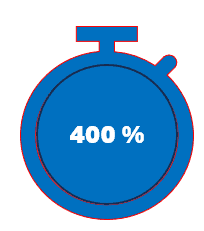
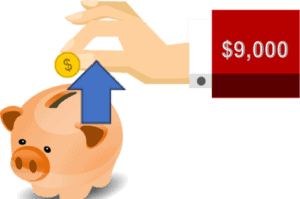
Bring us your challenges, we will bring you solutions. Feel The S&D Difference in your shop as well. See what products we offer at sdtool.com/line-card.